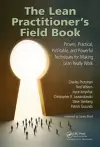
The Lean Practitioner's Field Book
6 authors - Hardback
£82.99
Charles Protzman formed Business Improvement Group (B.I.G.), LLC, in November 1997. B.I.G. is located in Baltimore, Maryland, and specializes in implementing Lean thinking principles and the Lean business delivery system—LBDS (trademark pending). Charles has over 31 years of experience in materials and operations management. He spent 13 years with AlliedSignal, now Honeywell, where he was an aerospace strategic operations manager and the first AlliedSignal Lean master. He has received numerous special-recognition and cost-reduction awards. Charles was an external consultant for DBED’s Maryland Consortium while he was with AlliedSignal. He had input into the resulting world class criteria document and assisted in the first three initial DBED world class company assessments. He is an international Lean consultant and has taught students courses in Lean principles and total quality worldwide. Charles spent the last 18 years implementing successful Lean product line conversions, kaizen events, and administrative business system improvements (transactional Lean) across the United States. He is following in the footsteps of his grandfather, who was part of the Civil Communications Section (CCS) of the American Occupation. Prior to Deming’s 1950 visit to Japan, C.W. Protzman Sr. surveyed over 70 Japanese companies in 1948. Starting in late 1948, Homer Sarasohn and C.W. Protzman Sr. taught top executives of prominent Japanese companies an eight-week course in American participative management and quality techniques in Osaka and Tokyo. Over 5100 top Japanese executives had taken the course by 1956. Many of the lessons we taught the Japanese in 1948 are now being taught to Americans as "Lean principles." The Lean principles had their roots in the United States and date back to the early 1700s and later to Taylor, Gilbreth, and Henry Ford. The principles were refined and expanded by Shigeo Shingo and Taiichi Ohno at Toyota. Modern-day champions are Norman Bodek, Jim Womack, and Dan Jones. Charles participated in numerous benchmarking and site visits, including a two-week trip to Japan in June 1996, where he worked with Hitachi in a kaizen event. He is a master facilitator and trainer in TQM, total quality speed, facilitation, career development, change management, benchmarking, leadership, systems thinking, high-performance work teams, team building, Myers–Briggs Styles indicator, Lean thinking, and supply chain management. He also participated in Baldridge Examiner and Six Sigma management courses. He was an assistant program manager during "Desert Storm" for the Patriot missile-to-missile fuse development and production program. Fred Whiton, MBA, PMP, PE, has 30 years of experience in the aerospace and defense industry, which includes engineering, program and portfolio management, strategy development, and operations. He is currently employed by DRS Technical Services as a division vice president responsible for clients in seven countries at over 50 locations. Fred has both domestic and international expertise within homeland security, command and control intelligence surveillance and reconnaissance sensors and services, military and commercial aerostructures, and defense systems supporting the US Navy, US Air Force, US Army, and Department of Homeland Security (DHS) across a full range of functions from marketing, concept development, engineering, and production into life cycle sustainment and logistics. Fred began his career as a design engineer at General Dynamics, was promoted to a group engineer at Lockheed Martin, and progressed to becoming a director at Northrop Grumman within the Homeland Defense Government Systems team. As vice president of engineering and operations at Smiths Aerospace, he was the Lean champion for a Lean enterprise journey, working closely with Protzman as the Lean consultant, for a very successful Lean implementation within a union plant, including a new plant designed using Lean principles. Fred has a BSME from the University of Maryland, an MSME from Rennselaer Polytechnic Institute, a master’s from The George Washington University, and an MBA from The University of Chicago. He is a professional engineer in the State of Maryland, is a certified project management professional (PMP), served as a commissioner on the State of Maryland Commission for Manufacturing Competiveness, served as a commissioner on the Maryland Commission on Autism, and is a member of the board of directors for multiple organizations, including the Regional Manufacturing Institute (RMI) with headquarters in Maryland. Joyce Kerpchar, PA-C, has over 28 years of experience in the healthcare industry and currently serves as the director of the Institute for Surgical Advancement at Florida Hospital Orlando, which is part of the Adventist Health System, an acute-care, tertiary hospital caring for more than 1.5 million patients a year. She joined Florida Hospital in 2001 and spent over five years as a senior consultant implementing Lean across the eight campuses in a variety of clinical departments, is a Six Sigma black belt, and is a certified MBTI instructor. Kerpchar began her career as a board-certified physician’s assistant in cardiovascular and thoracic surgery and primary care medicine.Prior to joining Florida Hospital, she held a variety of administrative positions in health-care-related industries, which included managed care operations and contracting for a PruCare/Prudential Healthcare that served 200,000 members in nine counties in Central Florida, product management for Avio Corporation, as a provider of information technology for ambulatory health-care organization, and as a partner in a consulting firm that specialized in business and market entry strategy for high-tech start-ups. Kerpchar is passionate about leveraging Lean in health-care processes to eliminate waste and reduce errors, to improve the overall quality, and to reduce the cost of providing health care. Christopher Richard Lewandowski, BS, MS, BB, has over 24 years of experience in operations and manufacturing engineering. He is currently the manufacturing engineering and VBLSS champion for ITT Enidine. Chris is an ITT-certified Lean master, Lean practitioner level 3, and Six Sigma black belt. He is leading the current Lean implementation at his facility and has delivered 40% to over 70% gains in productivity across all major product lines, resulting in over a million dollars in Lean savings and cost avoidance. He has led Lean implementations in manufacturing, materials, and office environments. He specializes in implementing Lean tooling solutions and creating single-piece machines in place of traditional monument and batch-type operations/machines. Chris began his career as a manufacturing engineer with Woodward HSC Aircraft Engine Systems, where he worked in new product development. He developed new processes to improve productivity and quality in addition to providing design input to improve the manufacturability of their products. He received his BS and MS in industrial technology from Buffalo State College. He has over 24 years of experience in providing design input to improve engineering, engineering management, and operations management. Steve Stenberg is a senior Lean sensei consultant and operates his own consulting business Continuous Progress, LLC, specializing in leadership coaching and organizational Lean transformation. He has over 27 years of experience in operations management and continuous improvement. Steve began his career at Donnelly Corporation, an automotive manufacturing company based in Holland, Michigan. Steve has held several leadership positions, including general manager, plant manager, manufacturing manager, advanced quality engineer, program manager, and senior Lean consultant. At Donnelly, he learned the fundamentals of people development and how the Scanlon principles work. In the mid-1990s, Donnelly began the transition to a Lean corporation while applying the Toyota production system methodologies. Donnelly became a model site for Lean transformation and benchmarking. Steve was very fortunate to have learned from some of the very best Lean experts during this period. Educated in industrial engineering and through the extensive teaching and learning of the Toyota production system, Steve formed his own consulting company in the early 2000s. He has developed a passion for applying TPS principles and teaching others the Lean philosophy. Steve has been applying Lean principles in various industries. He has extensive experience in aerospace, consumer goods, retail, and health care. He has taught Lean improvement techniques at organizations in Mexico, Canada, Ireland, Japan, China, the Czech Republic, and the United States. Patrick Grounds has 20 years of experience in the automotive industry and 7 years in academia in the automated systems, robotics, and manufacturing technology disciplines. He has been involved with multiple start-up organizations and has had various responsibilities for the development and integration of business operating systems for global operations while working for Ford Motor Company, Siemens Automotive, Siemens-Yazaki Systems Technologies, and Continental Automotive. He has held positions as executive director of program management, executive director of quality, director of operational excellence, director of quality systems North America, and director of technical operations. Pat spent seven years in academia as head of the Department of Engineering Technology and chair of the Automated Systems Engineering Technology and Robotics Engineering Technology programs at Lake Superior State University. The Robotics Engineering Technology program was the first ABETaccredited program of its kind in the United States. Pat has a master’s degree in electronics engineering, solid state physics, from the University of Michigan, Ann Arbor. He is a master black belt and received his initial introduction to Lean from Dr. Edwards Deming through attending five of the famous four-day seminars and participating in the Deming study group with Ford Motor Company. He is a strong believer in the concept of organizational learning and has extensive experience in the management of global cross-functional teams, multisite operating systems, and strategic initiatives. He is currently president of Pat Grounds and Associates Consulting and has worked globally with clients in automotive, oil and gas, health care, mining, and government.