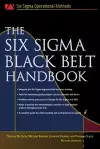
The Six Sigma Black Belt Handbook
6 authors - Hardback
£123.99
Michael Bremer has worked in the world of business process improvement since 1980. He led the creation of a company-wide improvement initiative for Beatrice Companies, a Fortune 30 Company at the time, where he had the opportunity to study under the tutelage of Dr. W. Edwards Deming and Dr. Joseph Juran. The Beatrice Improvement initiative was one of the models studied in creating the Malcolm Baldrige Quality Award. Michael is currently the president of the Cumberland Group. In recent years he has served as a Senior Engagement Manager for Motorola University, is a past Chief Financial Officer for the Association of Manufacturing Excellence and has held a variety of other positions in industrial and service businesses.
Michael currently teaches a class on innovation and process improvement for the University of Chicago’s Graham School. He co-authored Six Sigma Black Belt Handbook (McGraw-Hill, 2004) and Six Sigma Financial Tracking and Reporting(McGraw-Hill, 2005), aka: I had a million dollars in savings, but my P&L did not change. Michael earned a BS in accounting, from the University of Missouri – St. Louis. He is a CPA, certified MBB, certified Lean Bronze expert and a CMC. He has worked with organizations in many countries to improve the way they go about the business of improvement.
Brian McKibben is a founding partner of The Cumberland Group–Chicago. He has thirty years’ experience in operations planning and management, helping business teams reduce waste, improve quality, smooth production flows, shorten order cycle times, and reduce inventories. His approach to business performance improvement includes four elements:
Before joining Cumberland in 1991, Brian held management roles in several manufacturing companies. That experience and the insights he gained from them contribute to his effectiveness in a consulting role. Managing the manufacturing planning functions for 140 Beatrice U.S. Food plants and warehouses provided perspective on optimization of a large-scale enterprise while providing for autonomy and job satisfaction of local operating teams. Directing product design, manufacturing engineering, industrial engineering and manufacturing services for The HON Company, Wesco Manufacturing, and All-Steel proved that even complex processes like product and manufacturing process development can be streamlined (made Lean) to achieve results in a fraction of "expected" times. His experience in a turnaround situation confirmed the saying that "the impossible is often the untried," and that the technical issues in business are less important than the people issues. Business successes are the result of carefully nurtured teamwork; not the rah-rah fluff type, but rather the practical nuts-and-bolts approach that is focused on the team’s common goals and the mechanics of how they work together effectively to achieve those goals quickly.
Brian holds a BS in business and economics/industrial management from the Stuart School of Management and Finance at the Illinois Institute of Technology, Chicago. He is past president of the Chicago chapter of the Institute of Industrial Engineers, a speaker on operations planning and performance improvement to other professional organizations, and co-author of Six Sigma Financial Tracking and Reporting (McGraw-Hill, 2005).